Die Cast Mould Making: A Comprehensive Guide for Modern Manufacturing
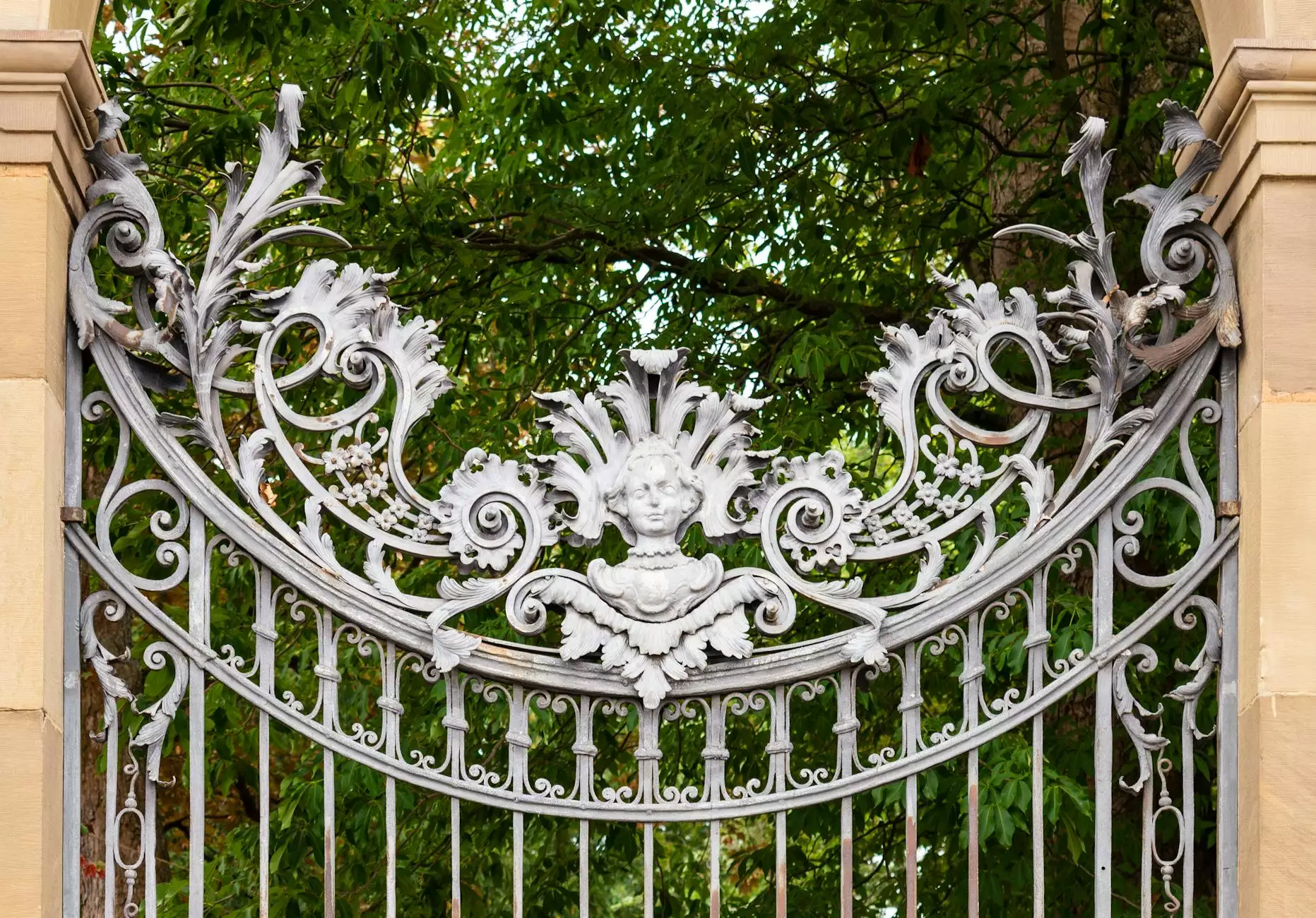
The realm of die cast mould making has undergone tremendous transformations over the years, becoming a cornerstone in modern manufacturing processes. At deepmould.net, we specialize in providing premium solutions catered to the needs of industries that rely on precision and durability. This article delves deep into the intricacies of die casting, the significance of mould makers, and how understanding this process can greatly benefit businesses across various sectors.
What is Die Cast Mould Making?
Die cast mould making is a manufacturing process that involves creating metal parts by pouring molten metal into a mould. The moulds are designed to produce specific shapes that meet high tolerance levels. This process typically utilizes materials like aluminum, zinc, and magnesium, which have become preferred choices for their excellent mechanical properties and lightweight nature.
The Die Casting Process Explained
The die casting process can be broken down into several key steps:
- Design & Engineering: Designing the mould is a crucial first step. Expert engineers create detailed drawings and simulations to ensure the mould will function correctly.
- Material Selection: Choosing the right metal alloy is fundamental. Different alloys offer various characteristics, such as strength, corrosion resistance, and thermal properties.
- Mould Creation: This involves precise cutting and shaping, usually via CNC (Computer Numerical Control) machines, to build the mould parts, which are then assembled.
- Melting & Pouring: The selected metal is melted at high temperatures and poured into the mould under high pressure.
- Cooling: After pouring, the metal rapidly cools and solidifies in the shape of the mould.
- Extraction: Finally, the solid product is removed from the mould. Post-processing may involve machining and finishing to achieve the final desired surface quality.
Why is Die Cast Mould Making Important?
The significance of die cast mould making in the manufacturing industry cannot be overstated. It offers several unparalleled advantages:
- Precision: The die cast process enables the production of components with extremely tight tolerances, ensuring high precision.
- Efficiency: High-speed production rates mean that large volumes of parts can be manufactured quickly.
- Cost-Effectiveness: Despite initial tooling costs, die casting proves economical for large-scale productions due to lower per-part costs.
- Material Versatility: Die casting accommodates various metals, allowing for product diversity that meets different customer needs.
Applications of Die Casting
The applications of die casting span diverse industries, including:
- Automotive: Components like engine blocks, transmission housings, and wheels are commonly produced using die casting techniques.
- Aerospace: Die casting is crucial for producing lightweight, strong parts for aircraft.
- Consumer Electronics: Items such as housings for laptops and phones often utilize die cast parts for better heat dissipation and aesthetics.
- Healthcare: Medical devices benefit from the precision and reliability of die cast components.
Choosing the Right Manufacturing Partner
Selecting an adept partner in die cast mould making is essential for achieving your production goals and maintaining product quality. Here are key factors to consider:
Experience and Expertise
A company with a long-standing history in die casting will likely possess the necessary knowledge to tackle complex projects efficiently. Check their portfolio and case studies to gauge their proficiency.
Technological Capabilities
Modern die casting relies heavily on technology, from CAD software for design to CNC for precision moulding. Partnering with a company that invests in the latest technology can drastically enhance production quality and efficiency.
Quality Assurance Measures
Quality control is vital in manufacturing. Ensure that the die casting partner has robust QA processes in place, adhering to industry standards. Certifications like ISO9001 can also be indicators of a commitment to quality.
The Future of Die Cast Mould Making
As industries evolve, so does the field of die cast mould making. New advancements are paving the way for:
- Smart Manufacturing: The integration of IoT (Internet of Things) and AI (Artificial Intelligence) in manufacturing processes will allow for real-time monitoring and adjustments during die casting operations.
- Enhanced Materials: Research into new metal alloys and composites is ongoing, promising lighter, stronger, and more resilient products.
- Sustainability: Efforts in recycling die cast scraps and reducing waste will significantly impact the industry's carbon footprint.
Conclusion
The field of die cast mould making is vast, intricate, and essential for modern manufacturing. With its profound influence on various industries, understanding this process and finding the right partner can offer significant advantages in terms of quality, efficiency, and cost. Explore more about how deepmould.net can assist you with high-quality die cast mould making solutions tailored to your unique business needs.
As we continue to innovate and adapt, embracing the future of manufacturing will ensure that your business remains competitive and well-equipped for the opportunities that lie ahead in die casting and beyond.