The Rise of Custom CNC Machining Manufacturers
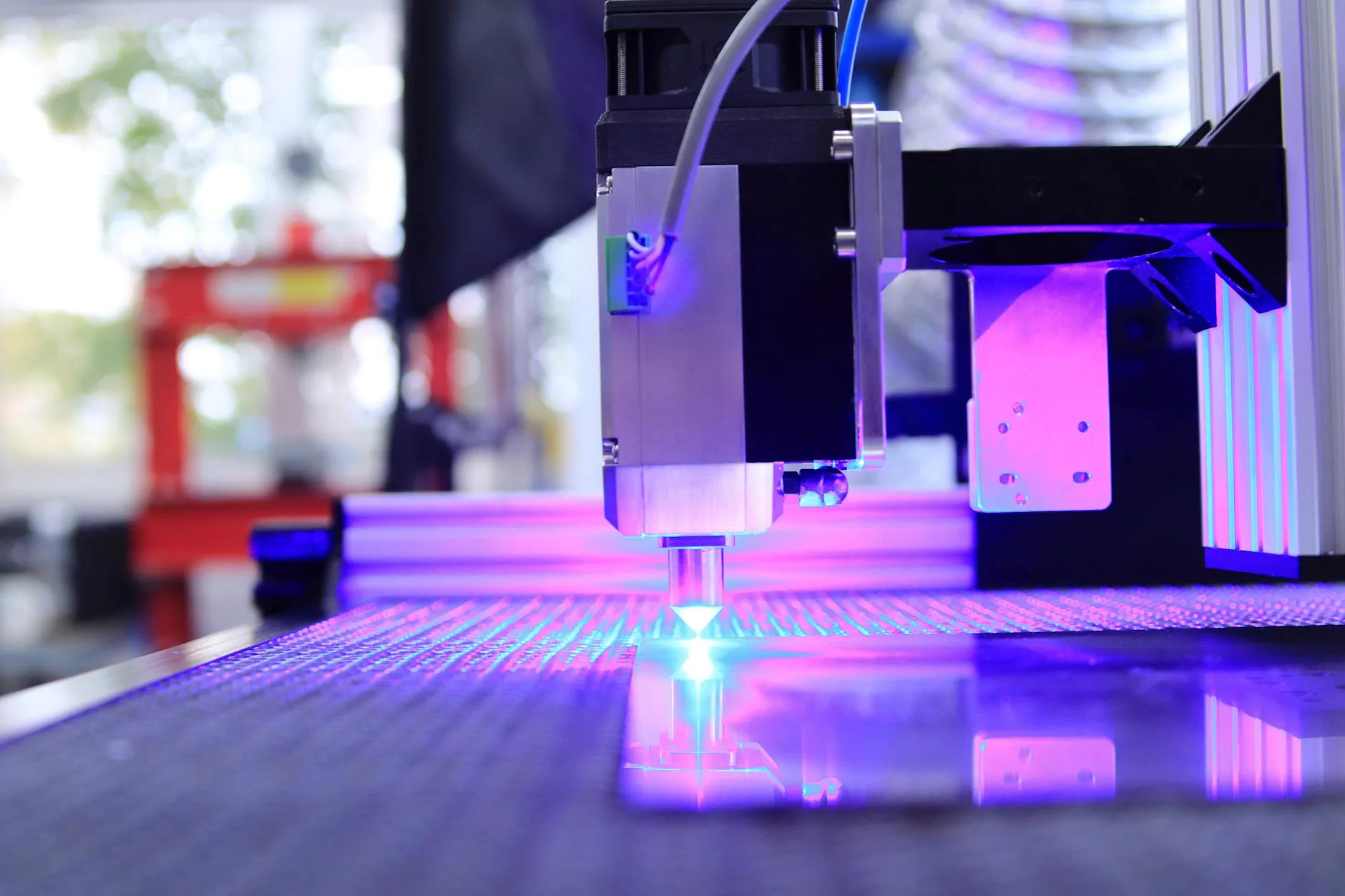
In today’s rapidly evolving manufacturing landscape, the role of custom CNC machining manufacturers has become increasingly pivotal. Companies are driven by the need for precision, efficiency, and customization in their components. CNC, or Computer Numerical Control, machining is at the forefront of modern manufacturing technologies, allowing for the production of intricate parts with remarkable accuracy.
What is CNC Machining?
CNC machining is a subtractive manufacturing process that uses computer-controlled tools to remove material from a solid block or workpiece. This technique is widely utilized across various industries, including aerospace, automotive, medical devices, and electronics. The primary advantage of CNC machining is its ability to produce complex shapes and designs that would otherwise be impossible or incredibly costly with traditional manufacturing methods.
Advantages of Using a Custom CNC Machining Manufacturer
The benefits of partnering with a reputed custom CNC machining manufacturer like DeepMould are manifold. Let’s delve into some of the significant advantages:
- Precision and Accuracy: CNC machines operate with incredible precision, often achieving tolerances of +/- 0.001 inches. This level of accuracy ensures that the components fit perfectly into the assembly, reducing rework and scrap rates.
- Customization: As a custom CNC machining manufacturer, DeepMould specializes in tailored solutions. Clients can specify unique dimensions, materials, and finishes, ensuring the products meet their exact specifications.
- Efficiency: CNC machining minimizes human error and maximizes production speed. Once the program is set, machines can run continuously, producing part after part with consistent results.
- Versatility: CNC machines can work with a wide variety of materials, including metals, plastics, and composites. This versatility makes them suitable for different applications and industries.
- Cost-Effectiveness: Although the initial investment in CNC machinery can be significant, the long-term savings due to reduced labor costs, material wastage, and production times often outweigh these upfront costs.
The Process of Custom CNC Machining
The journey from design to finished product in custom CNC machining involves several critical steps:
1. Design Development
The process begins with a detailed CAD (Computer-Aided Design) model. Designers create and iterate on their designs using sophisticated software, ensuring that every detail is accounted for before production begins.
2. Programming
Once the design is finalized, skilled programmers translate the CAD model into a machine-readable code, typically G-code. This code instructs the CNC machine on how to move, cut, and shape the material.
3. Material Selection
Choosing the right material is vital. Depending on the application, manufacturers might use aluminum, stainless steel, titanium, or plastic. A trusted custom CNC machining manufacturer can guide you in selecting the optimal material for your specific needs.
4. Machining
During the machining process, the machine follows the G-code to carve out the part from the raw material. This stage can involve various operations, including milling, turning, drilling, and grinding.
5. Quality Control
After machining, the components undergo rigorous quality control testing. This includes dimensional inspections, surface quality checks, and functional tests to ensure they meet the specified tolerances and performance standards.
6. Finishing
The final step may involve post-machining processes such as polishing, anodizing, or coating to enhance the part's performance and aesthetic appeal.
The Importance of Quality in CNC Machining
Quality assurance is a cornerstone of successful manufacturing. Partnering with a reliable custom CNC machining manufacturer ensures that stringent quality control processes are in place. DeepMould employs advanced inspection techniques, including:
- Coordinate Measuring Machines (CMM): For precise measurement of the part against its design specifications.
- Visual Inspections: To assess surface finish and detect any anomalies.
- Functional Testing: To verify that the part performs as intended in its final application.
Real-World Applications of Custom CNC Machining
The versatility of CNC machining enables it to cater to various sectors. Here are some of the notable applications:
Aerospace Industry
CNC machining plays a critical role in the aerospace sector, where components must meet extraordinarily high safety and performance standards. Parts for aircraft engines, structural components, and specialized tooling are commonly manufactured using CNC technology.
Medical Devices
The precision required in medical devices makes CNC machining indispensable. Custom implants, surgical instruments, and diagnostic equipment all benefit from the accuracy and reliability of CNC manufacturing.
Automotive Components
Automotive manufacturing has embraced CNC machining for producing everything from engine parts to custom interiors. The ability to produce intricate designs helps manufacturers innovate while keeping production efficient.
Consumer Electronics
In the tech world, CNC machining is used to create housing for electronic devices, brackets, and other components. The sleek designs and lightweight materials made possible by CNC processes are essential for modern electronics.
Why Choose DeepMould as Your Custom CNC Machining Manufacturer?
At DeepMould, we pride ourselves on being a leading custom CNC machining manufacturer. Our commitment to quality, precision, and customer satisfaction makes us the ideal partner for your manufacturing needs.
Expertise and Experience
With years of industry experience, our team of skilled engineers and technicians possesses the expertise to handle even the most challenging projects. We remain abreast of emerging trends and technologies in CNC machining to provide top-notch services.
State-of-the-Art Technology
DeepMould utilizes advanced CNC machinery and software, ensuring that we can produce high-quality parts with tight tolerances. Our investment in the latest technology guarantees that we remain competitive and capable.
Customer-Centric Approach
We prioritize our customers’ needs and work closely with them to deliver tailored solutions. From initial design consultations to post-production support, we are here to guide you at every step of the process.
Conclusion
As the demand for precision-engineered components continues to grow, the significance of choosing the right custom CNC machining manufacturer cannot be overstated. Partnering with a reliable and experienced manufacturer like DeepMould ensures that your projects are executed with efficiency and accuracy. Embrace the advantages of CNC machining and take your business to new heights by leveraging our expert services today!