The Future of Manufacturing: Leveraging Rapid Prototype Injection Molds
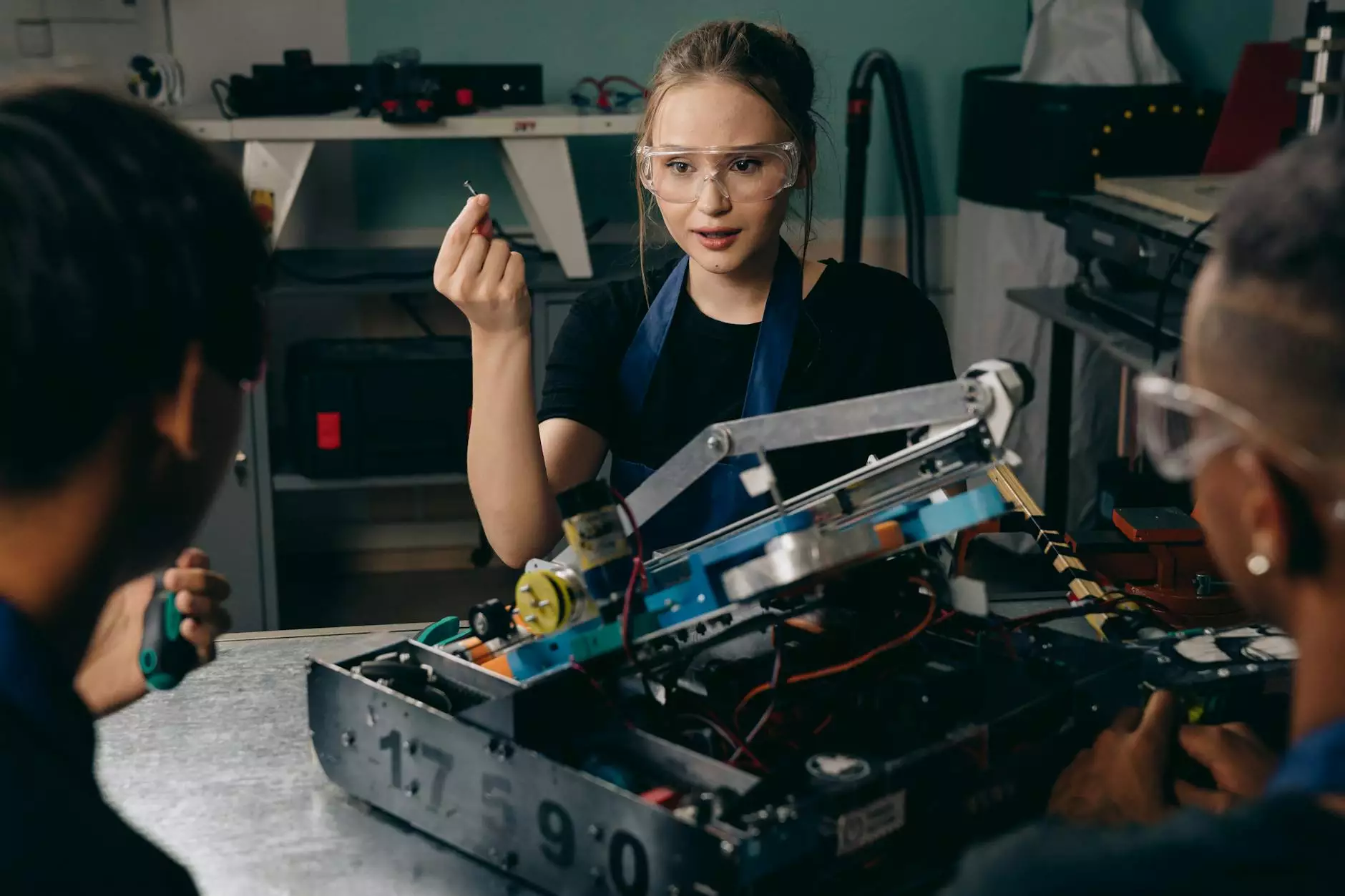
In the era of innovation and technological advancement, the manufacturing industry is experiencing a transformation like never before. One of the most groundbreaking techniques leading this transformation is rapid prototype injection molds. This method not only streamlines the manufacturing process but also enhances product development cycles. In this article, we delve deep into what rapid prototype injection molds are, their multitude of benefits, and how businesses can effectively integrate them into their operations.
Understanding Rapid Prototype Injection Molds
At its core, rapid prototype injection molding is a process used to create prototypes quickly using the injection molding technique. The goal is to develop a working model of a product that allows manufacturers to test, validate, and refine design concepts before moving into full-scale production.
What Is Injection Molding?
Injection molding is a manufacturing process where molten material is injected into a mold to create a particular shape. This method can be used for various materials, including plastics, metals, and ceramics. The process offers high accuracy and repeatability, making it a preferred choice for mass production.
The Rapid Prototyping Process
Rapid prototyping encompasses various techniques, but when it comes to injection molding, the process typically follows these steps:
- Design Creation: Using CAD (Computer-Aided Design) software, designers create intricate models of the intended product.
- Mold Fabrication: A mold is fabricated based on the design, often using 3D printing technology for speed and precision.
- Injection Molding: Molten material is injected into the mold, allowing the creation of the prototype.
- Cooling and Ejection: After cooling, the mold opens, and the prototype is ejected for inspection and testing.
Benefits of Rapid Prototype Injection Molds
Utilizing rapid prototype injection molds offers numerous advantages for businesses looking to enhance their manufacturing capabilities:
1. Faster Time to Market
One of the most significant benefits is the reduced time required to bring products to market. With traditional methods, designing and manufacturing prototypes can take weeks or even months. However, rapid prototyping accelerates this process, enabling companies to respond promptly to market demands.
2. Cost Efficiency
While the initial investment in rapid prototype injection molds may seem high, the long-term savings are substantial. By identifying design flaws early in the prototype phase, companies can avoid costly revisions during mass production.
3. Design Flexibility
Rapid prototyping allows for greater design flexibility. Companies can experiment with various materials and designs without committing to full-scale production, fostering creativity and innovation.
4. Enhanced Precision and Quality
The precision offered by injection molding translates to high-quality prototypes that closely resemble the final product. This precision is crucial for testing functionality and aesthetic appeal.
5. Early Testing and Validation
Rapid prototypes enable businesses to conduct early testing, gathering valuable user feedback before full-scale production. This iterative approach minimizes the risk of launching unsuccessful products.
Applications of Rapid Prototype Injection Molds
The versatility of rapid prototyping makes it applicable across various industries. Here are some notable applications:
- Automotive Industry: Designing parts for vehicles, such as dashboards and exterior trims, can be validated before the final production phase.
- Consumer Electronics: Prototyping enclosures for devices, ensuring that form and function meet user expectations.
- Medical Devices: Rapid prototyping allows for the swift development of complex devices, improving patient outcomes with faster product rollouts.
- Home Appliances: Testing new designs and features in appliances can lead to innovative products that meet consumer needs more effectively.
- Industrial Equipment: Manufacturing customized components that enhance performance and efficiency.
Integrating Rapid Prototype Injection Molds in Your Business
For businesses looking to implement rapid prototype injection molds, several strategies can facilitate integration:
1. Partner with a Reliable Manufacturer
Selecting a manufacturer with expertise in rapid prototype injection molds is crucial. Look for partners who embrace advanced technologies and have a proven track record.
2. Invest in CAD Technology
The quality of your prototypes largely depends on the precision of your design. Investing in high-quality CAD software and training your team can significantly enhance design processes.
3. Foster a Culture of Innovation
Encourage your team to experiment with new ideas. Provide them with the resources to test designs through rapid prototyping, which can stimulate creativity and lead to breakthrough products.
4. Utilize Feedback Mechanisms
Integrate user feedback into your prototyping process. Early testing with potential users can provide insights that drive design improvements and product success.
Challenges and Considerations
While the benefits of rapid prototype injection molds are significant, there are challenges that businesses may face:
1. Initial Setup Costs
Investing in the technology and equipment for rapid prototyping can be expensive. However, consider it a long-term investment that pays off through cost savings and increased efficiency.
2. Knowledge Gap
Staff may require training to effectively use new technologies and processes. Investing in training programs is essential for maximizing the benefits of rapid prototyping.
3. Material Limitations
Not all materials are suited for injection molding. Understanding which materials yield the best results for your designs is crucial to prevent production issues.
Conclusion
In conclusion, rapid prototype injection molds represent a significant leap forward in manufacturing processes. Not only do they shorten the product development cycle, but they also foster innovation and creativity while significantly reducing costs. As industries continue to evolve, leveraging these technologies can position businesses at the forefront of the marketplace. Companies like DeepMould.net exemplify the potential of using rapid prototyping to enhance design and production capabilities, paving the way for a future where efficiency and quality go hand in hand.
Start Your Journey Today!
To stay competitive in today's fast-paced market, adopting rapid prototype injection molds is no longer an option but a necessity. Explore how your business can implement these innovative solutions for unprecedented success!