Understanding High Pressure Die Casting Tooling
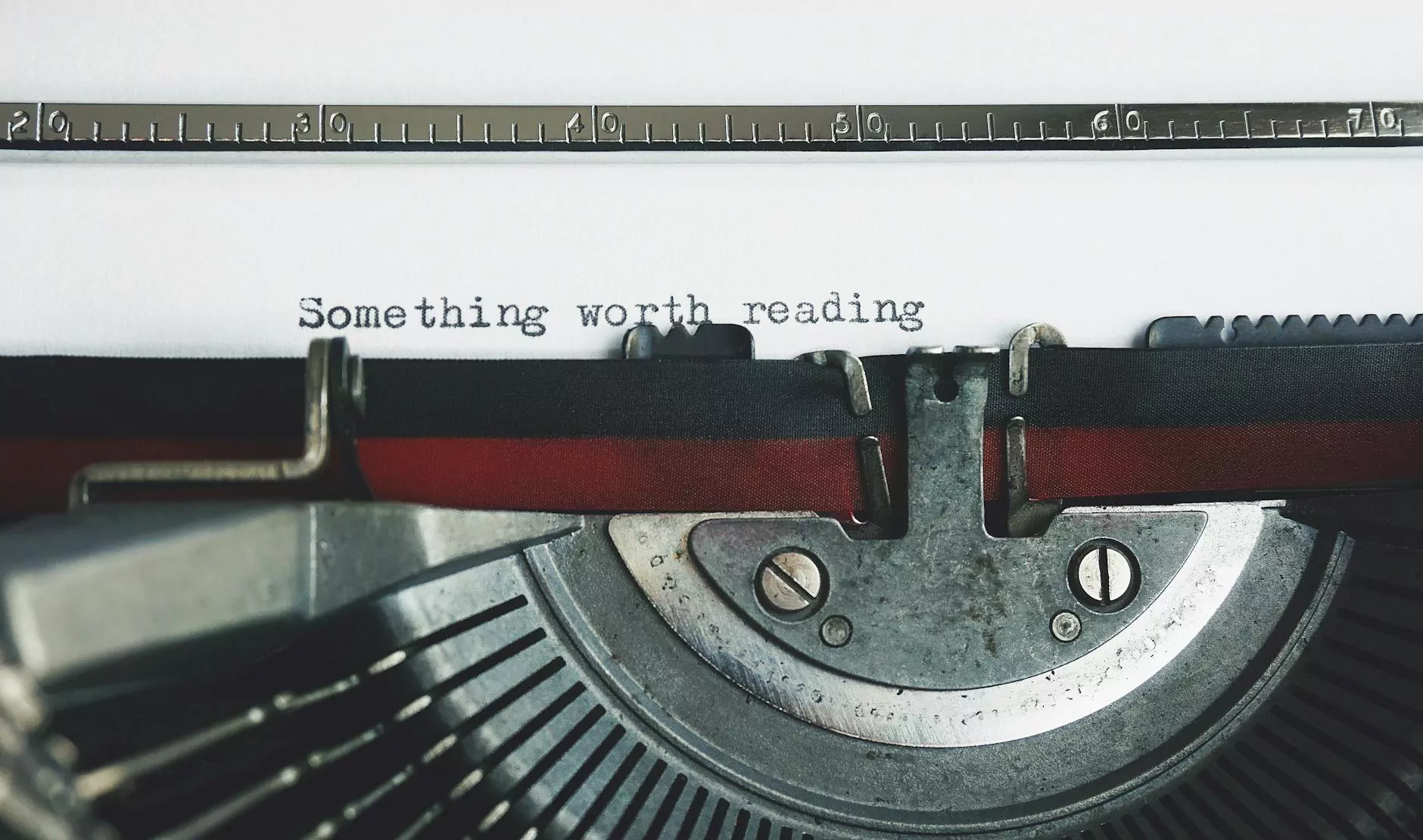
High pressure die casting tooling is a crucial component of the manufacturing process that ensures precision and efficiency. This method is widely used in the production of various metal parts across multiple industries, making it an essential topic for anyone involved in metal fabricators or manufacturing. High pressure die casting has gained popularity due to its capability to create complex shapes with high tolerances. In this article, we will explore the intricacies of high pressure die casting tooling, its advantages, and how it is revolutionizing modern manufacturing processes.
What is High Pressure Die Casting?
High pressure die casting is a manufacturing process that involves forcing molten metal into a mold under high pressure. The mold, typically made from durable materials like steel, allows for repeated use while maintaining its integrity over numerous cycles. This section will delve into more detail about the process and its applications.
Process Overview
- Preparation: The process begins with the preparation of the die, which consists of two halves – the stationary half and the movable half. These die halves are meticulously designed to form the desired part.
- Melting the Metal: Specific metal alloys, such as aluminum, zinc, or magnesium, are melted in a furnace to create molten metal.
- Injection: Once the metal reaches the appropriate temperature, it is injected into the die under high pressure, typically between 10 to 175 MPa.
- Cooling and Solidification: The molten metal cools rapidly once inside the die, solidifying into the desired shape.
- Die Opening and Ejection: After cooling, the die is opened, and the casting is ejected, ready for further processing.
The Advantages of High Pressure Die Casting Tooling
Choosing high pressure die casting tooling offers numerous benefits that make it a favorable option in the manufacturing industry:
1. Enhanced Design Flexibility
High pressure die casting allows for intricate designs and complex shapes that may not be feasible with other manufacturing processes. Manufacturers can benefit from the ability to design components that optimize performance without compromising structural integrity.
2. Improved Product Quality
One of the standout features of high pressure die casting tooling is its ability to produce high-quality components. With tight tolerances, minimal porosity, and superior surface finishes, parts produced using this method often require little to no secondary machining, thus reducing overall production time and costs.
3. Increased Production Efficiency
High pressure die casting is remarkably efficient due to its rapid cycle times. The process can churn out thousands of parts daily, making it ideal for high-volume needs. Additionally, the automation of the die casting machines contributes to the streamlined workflow, further enhancing efficiency.
4. Material Versatility
This method can utilize a variety of metals, making it suitable for multiple applications. Aluminum, zinc, magnesium, and copper alloys are commonly cast, each providing different properties that can be tailored to specific applications.
Applications of High Pressure Die Casting Tooling
The versatility of high pressure die casting tooling finds usage in various sectors. Here are a few notable applications:
- Automotive Industry: High pressure die casting is extensively used to produce engine blocks, transmission cases, and other critical components.
- Aerospace Sector: Lightweight parts that require high strength-to-weight ratios are often manufactured using this process.
- Consumer Electronics: Many electronic devices feature casings and other components created via high pressure die casting tooling.
- Industrial Machinery: Components such as housings and brackets are produced to meet the rigorous demands of industrial applications.
Design Considerations for High Pressure Die Casting Tooling
When designing components for high pressure die casting, specific considerations must be taken into account to maximize the benefits of the process:
1. Draft Angles
Incorporating appropriate draft angles helps in the easy removal of the casting from the die, reducing the risk of damage and ensuring a smoother process.
2. Wall Thickness
Uniform wall thickness is critical in ensuring consistent cooling and reducing stresses in the final product. This helps avoid potential defects and maximizes the structural integrity of the casting.
3. Ribs and Features
Adding ribs can improve stiffness and strength without adding excessive weight. However, care should be taken to ensure that these design elements do not complicate the ejection of the part.
Advantages of Choosing DeepMould for High Pressure Die Casting Tooling
When it comes to sourcing high pressure die casting tooling, DeepMould.net stands out as a leader in the field. Here are a few reasons why partnering with DeepMould can benefit your business:
1. Expertise and Experience
With years of experience in the metal fabricators industry, DeepMould has developed unrivaled expertise in designing and manufacturing high pressure die casting tooling.
2. State-of-the-Art Technology
DeepMould employs the latest technologies and techniques in die casting, ensuring precision and quality in every project.
3. Custom Solutions
They offer tailored solutions to meet specific project requirements, ensuring that clients receive the best tooling for their unique applications.
4. Commitment to Quality
Quality assurance is paramount at DeepMould. Rigorous testing and inspection processes are in place to ensure that every tooling solution meets high standards before it reaches the customer.
Challenges in High Pressure Die Casting Tooling
While high pressure die casting has numerous advantages, it also presents certain challenges that manufacturers must navigate:
1. Initial Tooling Costs
The upfront costs for creating high-quality die casting tools can be significant. However, these costs are often amortized over large production runs.
2. Tool Wear and Maintenance
Die tooling can experience wear and tear over time due to the high-pressure environment, necessitating regular maintenance to ensure longevity and performance.
Future Trends in High Pressure Die Casting Tooling
As technology progresses, high pressure die casting tooling is poised for several exciting advancements:
1. Smart Manufacturing
The integration of IoT and AI in manufacturing is revolutionizing processes, enabling predictive maintenance and real-time monitoring of die casting operations.
2. Sustainable Practices
More manufacturers are focusing on sustainable practices, including the recycling of materials and reducing waste to enhance the environmental footprint of die casting.
3. Advanced Materials
Development in metallurgical science is leading to the creation of new alloys that offer superior properties, enhancing the capabilities of high pressure die casting.
Conclusion
In conclusion, high pressure die casting tooling is a vital aspect of modern manufacturing, offering countless benefits, including design flexibility, improved product quality, and increased production efficiency. Companies like DeepMould.net are paving the way for advancements in this field, making them an ideal partner for any business looking to elevate its manufacturing processes. As we move towards a more technologically advanced and sustainable future, the role of high pressure die casting will only continue to grow, making it an essential topic for professionals in the manufacturing and metal fabricators industries.